LFP Inox
Specifications
Details
Continuous, hygienic measurement of liquids – even at higher temperatures.
The LFP Inox is a hygienic level sensor for liquids using TDR technology – a process for determining the time of flight of electromagnetic waves. The time difference between the sent pulse and the reflected pulse is used to generate a level signal, both as a continuous value (analog output) and a freely positionable switching point (switching output). The use of FDA-compliant materials in an EHEDG-certified design means that the LFP Inox can be relied upon for optimum and unrestricted cleaning, even in applications with the most stringent hygiene requirements. Its modular connection system allows simple and flexible installation in any application. Thanks to high temperature and pressure resistance, unrestricted use is possible under CIP and SIP conditions. This impressive profile is topped off with communication capability via IO-Link to the superordinate control units.
LFP Inox AT A GLANCE
Benefits:
- Rugged design increases service life
- High flexibility – rod probe can be cut to length and connection concept is interchangeable
- Cost savings as a result of multiple output signals: one system for both point level and continuous level measurement
- Maintenance-free and easy to commission without calibration, saving time and money
- Remote display of measured values and saves space
Features
- Level measurement in hygienic applications
- Rod probe can be cut to size manually up to 4,000 mm in length with Ra ≤ 0.8 µm (optionally with Ra ≤ 0.4 µm)
- Process temperature up to 180 °C, process pressure up to 16 bar
- CIP/SIP-resistant
- High enclosure rating IP 67 and IP 69
- Interchangeable hygienic process connections
- 3 in 1: combines display, analog output, and binary output
- Remote amplifier with process connection, autoclavable
- IO-Link 1.1
Advantages
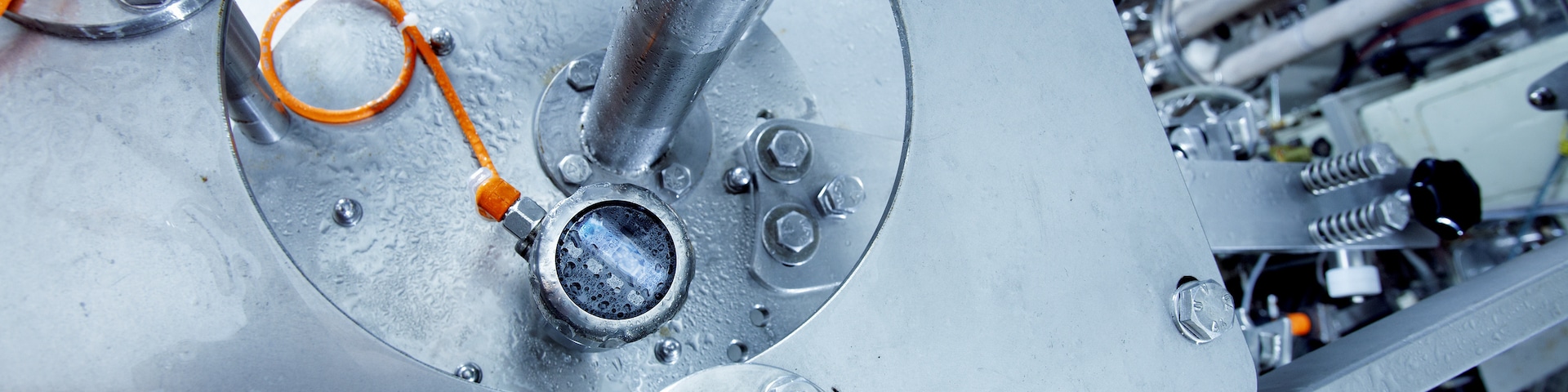
Precise level measurement and point level measurement in hygienic applications
The LFP Inox level sensor combines high performance with hygienic design. This device can be used to continuously measure both level and point levels. The sensor switching points for this are freely definable. Thanks to multiple output signals, it is possible to measure fill and point levels either together or separately. The rugged sensor is ideal for use in CIP and SIP applications in food and beverage production as well as in the pharmaceutical industry. Whether viscous, sticky or deposit-forming – LFP Inox measures all liquids reliably. With its intelligent “foam blanking” function, the sensor can even measure levels in highly foaming media.
.png)
Hygiene and performance go hand-in-hand with the LFP Inox and ensure a high reliability.
The right solution for many installation situations
Whether in the tank or in the bypass: Thanks to the variety of process connections and numerous accessories available, the LFP Inox can be integrated into many different applications. The fast and simple commissioning of the sensor via the integrated display involves hardly any cost. And in conjunction with a coaxial tube, the probe of the sensor delivers very accurate values even for measurements in plastic tanks. The rod probe can be shortened as needed – and can therefore be ideally adapted to the specific requirements of an application.
High flexibility and numerous application possibilities.
Special variants for the pharmaceutical industry
SICK also offers the LFP Inox in a variant that caters to the special requirements of pharmaceutical applications. The hygienically designed sensor has a gap-free PEEK seal that completely separates the process from the sensor and corresponds to enclosure rating IP69. The seal is also rugged, temperature insensitive and chemically resistant. To enable you to meet your documentation obligations, the devices come with a 3.1 Material Certificate as well as a calibration certificate.
.png)
End-to-end safety – in particular for demanding pharmaceutical applications.
View more about LFP Inox on main site